
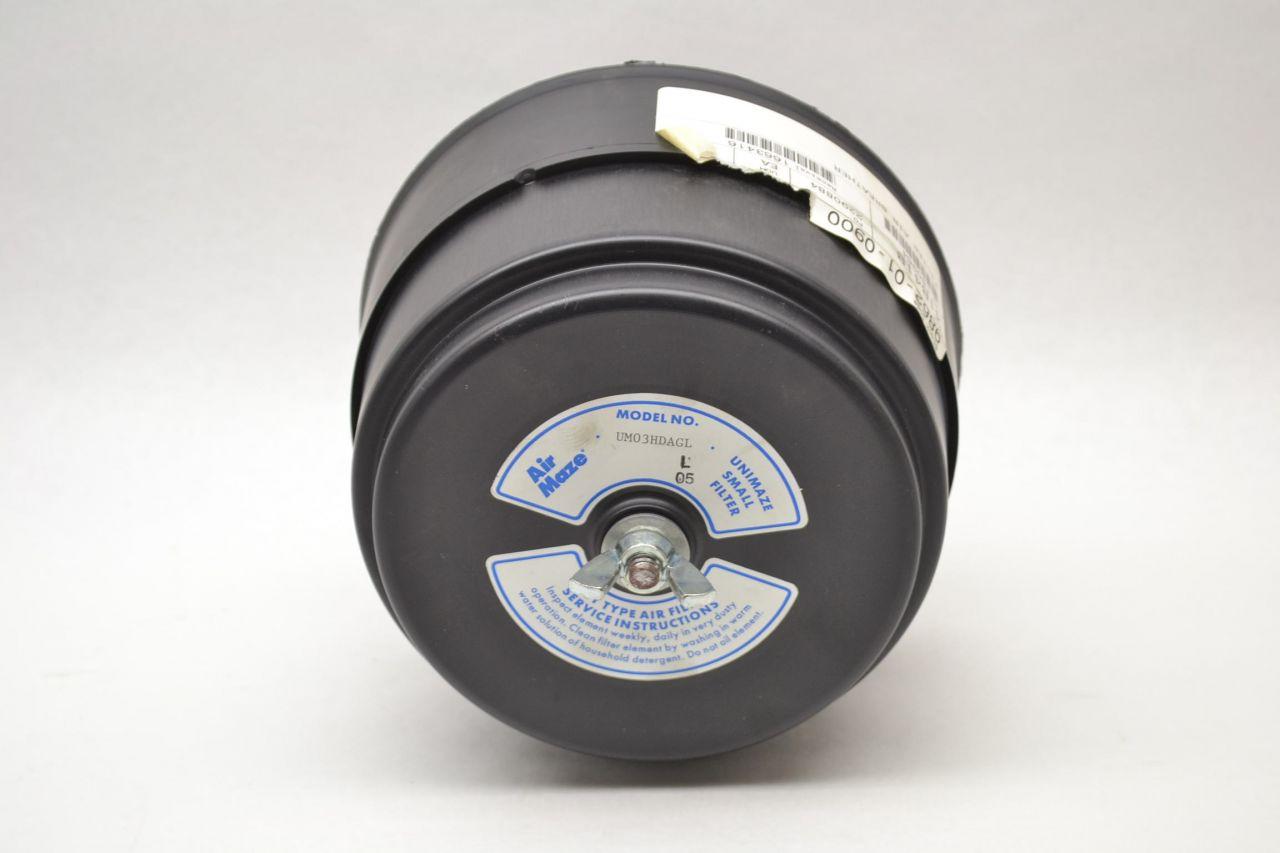
One can then be used to make CO while the other is rejuvenating and producing oxygen. The trick to making things efficient is to plumb two reaction chambers into the system. But this, too, can be recycled through the reaction chamber. When the oxygen is used to make steel, that also emits carbon dioxide. This creates a low-oxygen environment inside the chamber, encouraging the BCNF1 to release its oxygen. That works by taking nitrogen emitted from the blast furnace and pumping it through the reaction chamber. After about a day, the BCNF1 becomes saturated with oxygen atoms, and so has to be rejuvenated. When the recycling system pumps the CO 2 through the reaction chamber, the BCNF1 grabs oxygen atoms from the gas and absorbs them into its crystalline structure, leaving behind CO. The result is Ba 2Ca 0.66Nb 0.34FeO 6 (BCNF1, to its friends). Drs Ding and Kildahl made their version by grinding up barium carbonate, calcium carbonate, niobium oxide and iron oxide, mixing the resulting powders, and then baking the mixture in an oven. Further variants are employed in fuel cells and other clean-energy systems. Another can produce phone screens that are almost unbreakable. One type is used to make solar panels more efficient. Researchers are finding a variety of roles for perovskites.

The name has now been generalised to refer to a group of materials which share this mineral’s distinctive crystal structure without necessarily sharing its chemical composition. The original perovskite was a mineral discovered in the Ural mountains, in Russia, in 1839, and named after Count Lev Perovski, a mineralogist from that country. This sits in a reaction chamber at the heart of the recycling system. What makes all this possible is an intriguing material called a perovskite. The oxygen thus released can then be used in the second part of the steelmaking process, in which that gas is blown through molten iron in a differently designed furnace, to burn off part of the carbon now dissolved in it and arrive at the optimum ratio of iron to carbon to create the type of steel required. It is made by capturing the CO 2 produced in the furnace and recycling it by splitting it into CO and oxygen. The clever bit is where this gas comes from. The modification Drs Ding and Kildahl propose (see diagram) cuts coke out of the loop by pumping CO directly into the blast furnace.
